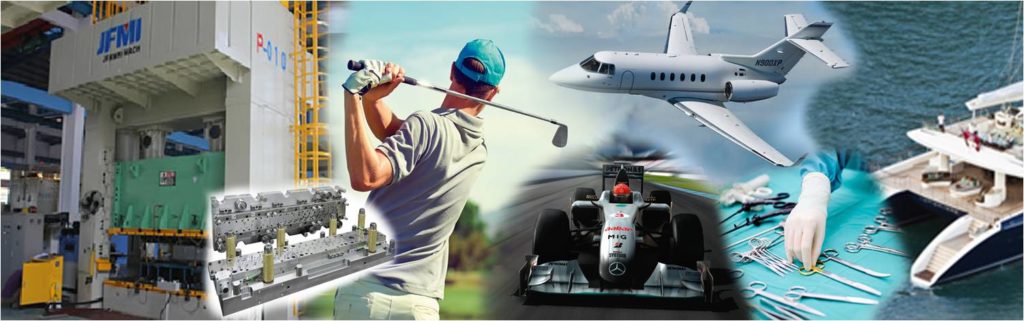
PROJECTION THERMIQUE POUR L'INDUSTRIE ....
...du laboratoire à la fabrication industrielle.
PRINCIPE DE LA PROJECTION THERMIQUE
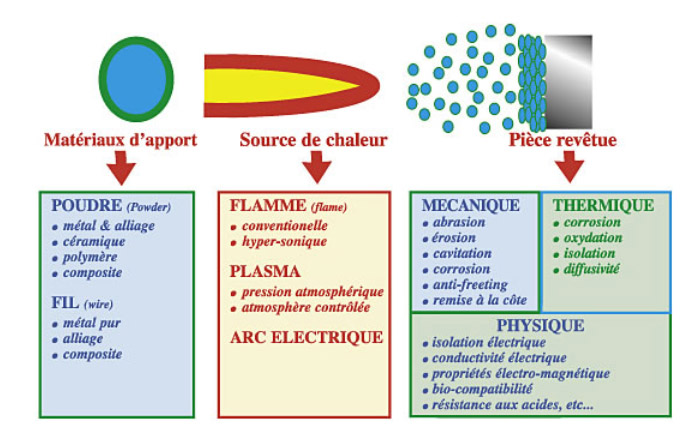
Il peut s’agir de projection par plasma, de projection par flamme (conventionnelle ou HVOF) ou de projection par arc électrique ; dans tous les cas le principe est le même, seules diffèrent les températures de traitement. La projection par flamme est bien adaptée pour la réalisation de dépôts de matériaux bas point de fusion (les thermoplastiques et certains métaux par exemple), la projection par arc électrique est utilisée pour la réalisation de revêtements à base de matériaux conducteurs électriques, la projection par plasma est adaptée aux matériaux très réfractaires comme les céramiques oxydes par exemple.
Le procédé de projection se déroule de la façon suivante :
- Le matériau du revêtement désiré est injecté dans une source chaude (flamme, plasma ou arc électrique) sous forme pulvérulente ou sous forme de fil,
- Le matériau est alors fondu sous forme de fines gouttelettes qui sont alors projetées sous l’effet du débit de gaz de la source chaude pour aller s’écraser à grande vitesse sur le substrat à revêtir,
- Celles ci se refroidissent extrêmement rapidement en cédant leurs calories au substrat ou aux couches précédemment déposées,
- L’accrochage avec le substrat est très intime si celui-ci a été préalablement préparé.
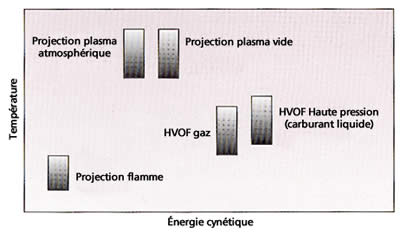
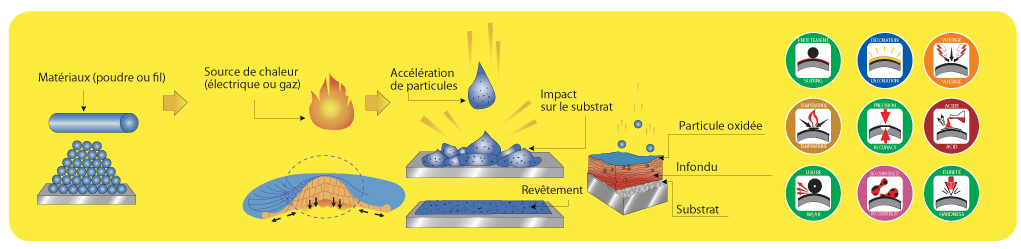
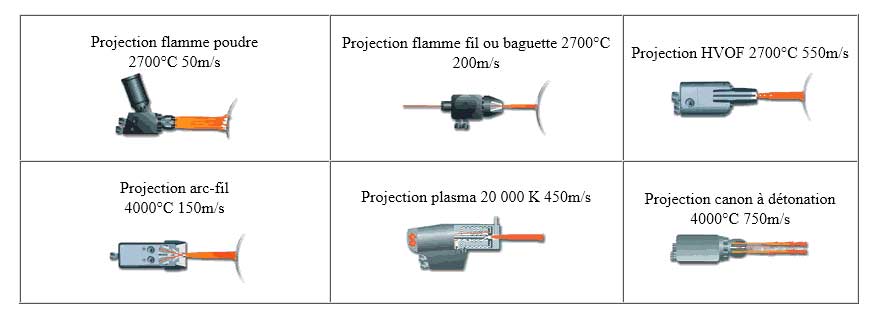
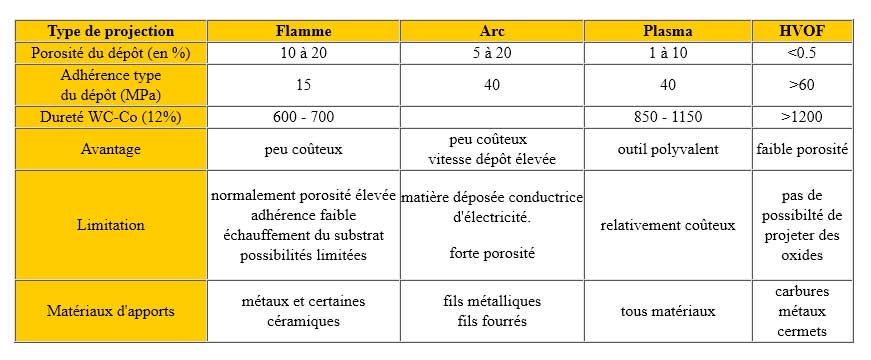
PROJECTION PLASMA
Un plasma est un gas ionisé constitué d’électrons libres, d’ions, d’atomes et de molécules dans des états excités ou non. C’est à cause de ses propriétés uniques qu’on l’a baptisé le 4éme état de la matière. Un plasma est généré lorsque l’on apporte à un gaz suffisamment d’énergie pour qu’il s’ionise.
Une torche plasma (voir figure suivante) est constituée de deux électrodes refroidies par un circuit d’eau, appelées anode et cathode portées respectivement aux potentiels positif et négatif et entre lesquelles est injecté un gaz. Un arc électrique créé par une décharge haute fréquence entre les deux électrodes permet de ioniser le gaz plasma (généralement un mélange argon-hydrogène) et créer le plasma qui est alors entretenu par le courant continu passant de la cathode à l’anode. Les poudres du matériau projeté sont alors introduites via un gaz porteur (argon en général) dans le jet de plasma ainsi constitué où elles sont fondues et accélérées avant d’aller s’écraser sur le substrat. Le jet de plasma est caractérisé par des températures très élevées (jusqu’à 20 000 °K au coeur du jet) et des coefficients de transfert thermique élevés pour permettre la fusion des particules de poudres.
Le procédé de projection plasma est le plus souvent utilisé à la pression atmosphérique, on parle alors de projection APS. Pour certaines applications référencées VPS et LPPS, le procédé de projection plasma est réalisé dans un environnement protégé dans des chambres où le vide est fait et parfois accompagné avec le remplissage d’un autre gaz à faible pression.
La projection plasma a l’avantage d’être un procédé versatile capable de fondre des matériaux à haut point de fusion comme des métaux réfractaires tel le tungstène ou des céramiques telle la zircone.
Un désavantage du procédé est qu’il cher d’investissement et complexe.
La technique de projection plasma a pour caractéristiques essentielles :
- La source d’énergie est séparée du substrat qui est maintenu à des températures de l’ordre de 20 à 100 °C : cela permet par exemple de déposer une céramique sur un polymère. Le substrat peut également être chauffé jusqu’à 900-1000 °C, en atmosphère contrôlée ou réduite, pour améliorer l’adhésion et la densification des dépôts métalliques,
- Les particules en vol interfèrent chimiquement et physiquement avec le gaz plasma et le gaz ambiant pompé par le jet ; le dépôt obtenu n’a pas nécessairement la même composition que les particules de départ (et présente ainsi des propriétés uniques),
- Le dépôt est formé particule par particule, et possède une structure plus ou moins lamellaire (voir figure suivante),
Les particules sont refroidies très brutalement lors de l’impact (vitesses de refroidissement de l’ordre de à K/s, ce qui peut créer des phases métastables, voir vitreuses, et permet des tailles de grain de l’ordre de 0,25 à 0,5 microns notamment pour les métaux et alliages. La technique de dépôt combine donc en une seule opération la fusion, la trempe et la consolidation, - Cette technique possède une grande souplesse d’utilisation ; en particulier les débits de gaz et la puissance peuvent être modulés indépendamment l’un de l’autre. En plus d’une grande reproductibilité des dépôts, il est possible de revêtir avec l’aide de robots sophistiqués des pièces de formes très complexes.
PROJECTION HVOF
La projection HVOF est un procédé de projection flamme à hautes vitesses. Au début des années 1980 Browning et Witfield, en utilisant la technologie des moteurs de fusées, ont introduit une nouvelle méthode de projection par procédé hautes vitesses destinée à la réalisation de revêtements métalliques.
Il existe différents types de pistolets HVOF ; ils se différencient par la technique utilisée pour obtenir des grandes vitesses. Une méthode consiste à utiliser une chambre de combustion refroidie par un circuit d’eau sous pression ainsi qu’une tuyère allongée. Le carburant liquide ou gazeux (white spirit, kérosène, hydrogène, propylène) est alors injecté sous pression dans la chambre avec l’oxygène, la combustion génère une flamme à haute pression qui va s’échapper par la tuyère et ainsi acquérir de la vitesse. La poudre à projeter peut alors être injectée axialement dans la chambre de combustion du pistolet ou alors être introduite radialement dans le cas de tuyères de laval où la pression est moins élevée. Le diagramme suivant illustre ce principe.
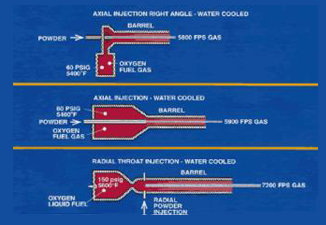
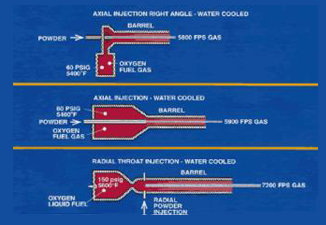
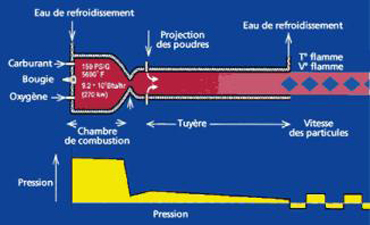
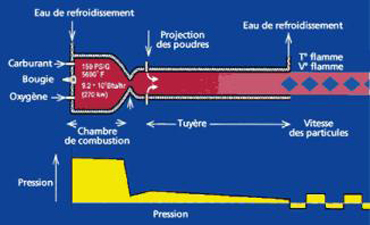
Une autre méthode utilise un système simple constitué d’une tuyère brûleur avec une buse accélérateur. Le carburant gazeux (propane, propylène or hydrogène) et l’oxygène sont introduits à haute pression, la combustion a lieu en sortie de la buse brûleur où souffle de l’air comprimé qui « pince » et accélère la flamme et refroidie en même temps le pistolet. La poudre est injectée axiallement par le centre du pistolet. Ce principe de fonctionnement est illustré sur le diagramme suivant.
Les revêtements HVOF sont très denses, durs et avec peu de contraintes résiduelles de traction, dans certains cas le revêtement peut même être en compression, ce qui permet l’obtention de revêtements épais, ce qui est peu possible avec les autres procédés de projection.
Les particules de poudres impactent sur le substrat à revêtir avec une très grande énergie cinétique et n’ont pas besoin d’être complètement fondues pour réaliser un revêtement de bonne qualité. C’est un avantage certain qui est exploité pour la réalisation de revêtements d’excellente qualité à base de cermets carbure.
Les paramètres qui influeront sur la qualité des revêtements seront les pressions carburant/comburant, les débits relatifs oxygène/carburant, le débit de gaz porteur des poudres, la distance de projection et la géométrie de la tuyère de projection. Tout ceci avec la règle que les plus grandes vitesses permettront d’avoir une meilleur adhésion, une meilleur cohésion des particules avec une densité des revêtements accrue.
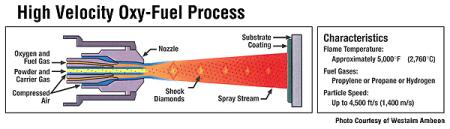
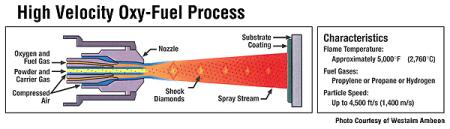
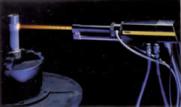
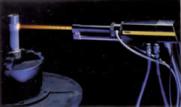
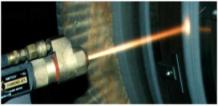
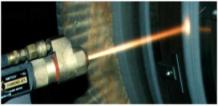
Pistolet HVOF en fonctionnement
PROJECTION FLAMME
PROJECTION FLAMME POUDRE
La projection flamme poudre est certainement le procédé le plus simple de tous les procédés de projection thermique. Il consiste à introduire une poudre à travers l’orifice central d’une buse-brûleur, la poudre fond et est entraînée par les gaz oxygène-carburant (généralement oxygène-acétylène ou oxygène-hydrogène) sur la pièce à revêtir. Ce système de projection est peu énergétique. Les revêtements réalisés par ce procédé contiennent un taux d’oxydes élevé ainsi qu’une forte porosité pouvant approcher 20%. La qualité des revêtements dépend aussi de la qualité des poudres. Le principe de fonctionnement d’un tel pistolet est illustré sur la figure suivante. L’utilisation de débit-litres pour contrôler les débits de gaz est un facteur important.
Un des principaux avantages des pistolet de projection flamme poudre par rapport au pistolet de projection flamme fil est lié à la plus grande variété de revêtements disponibles due au fait que la plupart des matériaux sont disponibles sous forme de poudres. Le procédé de projection flamme poudre est seulement limité par les matériaux qui ont une température de fusion supérieure à celle de la flamme ou alors dans le cas où le matériau projeté se décompose à la chaleur. Des revêtements de polymères (PTFE, PA12, …) peuvent aussi être réalisés par projection flamme.
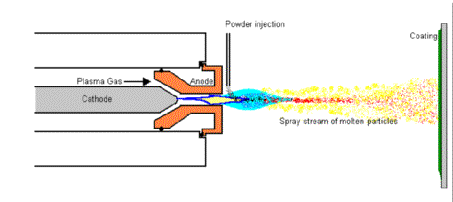
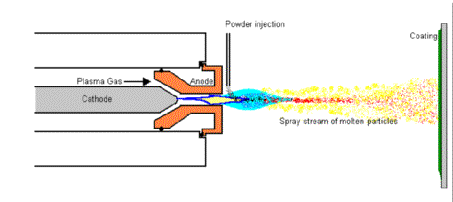
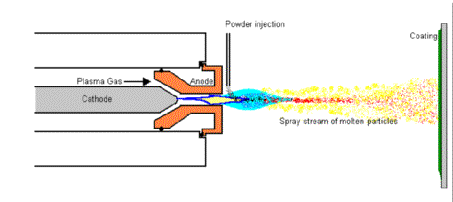
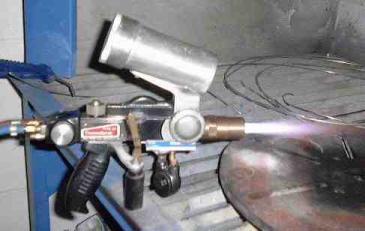
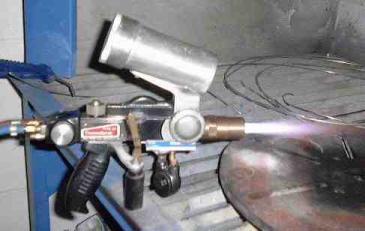
PROJECTION FLAMME FIL
La projection flamme fil, plus connue sous le nom de métallisation ou shoopage a été inventée en 1910 par la suisse Schoop qui a développé le premier pistolet de projection thermique de fils métalliques. L’appareil consistait en un brûleur dans lequel un carburant, acétylène ou hydrogène, était mélangé avec de l’oxygène pour créer une flamme en sortie de tuyère de brûleur. Un jet d’air comprimé entourant la flamme atomisait et propulsait le métal fondu. La continuité du procédé dépendait de l’approvisionnement du fil dans la flamme avec une vitesse contrôlée de façon à le fondre et le projeter avec un flux continu.
Schoop résolut ce problème en utilisant une turbine qui actionnait un système d’engrenages et de molettes qui tirait le fil dans la tuyère du brûleur. Cette appareillage lui apparu similaire à un pistolet, depuis c’est pour cette raison que l’on parle de « pistolets » de projection thermique et rarement de « torche ». Le principe de fonctionnement d’un tel pistolet est illustré sur la figure du dessous. Le concept de Schoop basé sur la projection de métal sous forme de fil correspond au démarrage de l’industrie de la projection thermique.
On peut constater que de nos jours le pistolet de projection flamme fil n’a que peu changé par rapport à celui utilisé du temps de Schoop. Bien qu’il y a eu des changements au niveau de la géométrie de la buse du brûleur et de l’injecteur d’air, le remplacement de la turbine à air par un moteur électrique, le principe reste le même système « tirer-pousser un fil dans une flamme, le fondre et l’atomiser et déposer les gouttelettes de métal fondu sur le support pour le revêtir avec un dépôt adhérent ».
Ce type de procédé de projection thermique a été très largement utilisé et l’est encore aujourd’hui pour les travaux de réparation d’éléments de machine et la protection contre la corrosion. Ses avantages sont qu’il est d’un investissement faible, il est facile d’utilisation en permettent l’obtention de rendements de projection élevés, c’est un système portable qui peut être utilisé en chantier. Ses désavantages sont qu’il est limité à la projection de matériaux existant sous forme de fil et le procédé ne permet pas l’obtention de revêtements à haute densité, avec un taux d’oxyde faible et une grande adhérence.


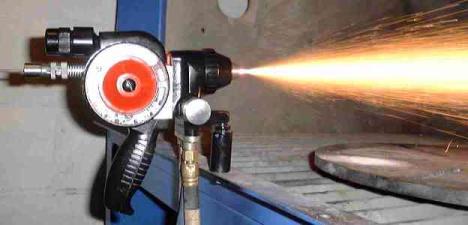
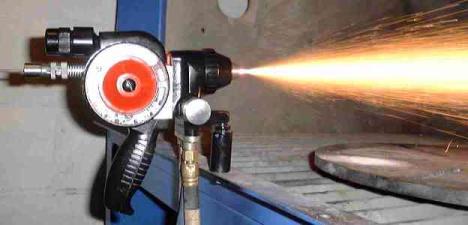
PROJECTION FLAMME BAGUETTES CERAMIQUE
La projection flamme de baguettes en céramique date du début des années 50 au moment de la demande de revêtements réfractaires résistant à la chaleur. La projection plasma était très peu développée et les revêtements obtenus par projection flamme à cause de leur forte porosité et leur faible cohésion ne pouvaient répondre aux besoins demandés. La solution fut « assez simple » ; Coors Ceramic et Norton développèrent des baguettes céramiques sous le nom de Rokide et pendant le même temps Metallizing Engineering Company (Mogul) modifia un pistolet de métallisation flamme fil pour projeter les baguettes. La modification portait essentiellement sur le design des mollettes de guidage pour pincer les baguettes céramiques et les faire avancer dans la flamme du brûleur, le principe de fonctionnement du pistolet développé par Schoop restant inchangé, la flamme étant concentrique au fil ou à la baguette de céramique pour assurer une parfaite fusion uniforme du matériau projeté. Un flux d’air comprimé soufflant autour de la flamme atomise le matériau fondu et le projète sur la pièce à revêtir. La vitesse des particules dans le procédé de projection de baguettes céramiques (tout comme dans la cas de la projection flamme fil) est de l’ordre de 185 m/s, ce qui conduit à des revêtements de densité voisine de 95 %. Les compositions des céramiques disponibles sur le marché incluent les zircones stabilisées, l’alumine, les spinelles, la mullite ou l’oxyde de chrome.
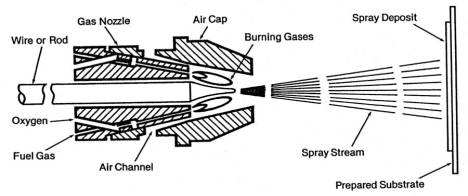
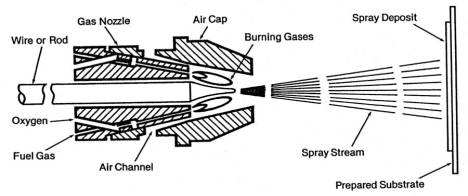
PROJECTION ARC FIL
Le procédé de projection arc-fil ou arc-électrique consiste à créer un arc électrique entre deux électrodes consommables du matériaux du revêtement pour le fondre et ensuite par l’intermédiaire d’un gaz à atomiser et projeter sur le support à revêtir la gouttelette de métal fondu.
Le pistolet est relativement simple. Deux guides dirigent les fils au point d’arc. Derrière ce point une buse dirige un jet d’air ou de gaz sous pression pour atomiser le métal fondu et le projeter sur la pièce à revêtir. Ce principe est illustré sur le diagramme suivant. Des générateurs fonctionnant à 450 ampères peuvent projeter jusqu’à 40 kg/h de matière. Les systèmes de projection arc électrique sont approvisionnés en fil avec des moteurs pneumatiques ou électriques ; des systèmes « tiré poussé » ou « poussé » existent sur le marché.
Les facteurs influençant la qualité des revêtements sont d’une part le matériel de projection utilisé et d’autre part la qualité du fil utilisé (finition, dureté, tension, composition chimique exacte et diamètre). Un diamètre de 1,6 mm est recommandé (pour l’utilisation d’un pistolet classique) car il permet une bonne finition avec un débit d’air pas excessif.
Un avantage de cette technique de projection peut être la possibilité de projeter deux fils de compositions différentes pour obtenir des pseudo alliages. Un exemple est, en travaillant avec une bobine de fil cuivre et une bobine de fil étain, la réalisation de revêtements d’alliage cuivre étain avec une parfaite distribution homogène des deux constituants dans le revêtement. Aussi le développement des fils fourrés a permis la réalisation de revêtements d’alliages complexes comme les MCrAlY ou les alliages contenant des carbures.
La projection arc-fil est une technique plus souple que la projection plasma. Les avantages d'une telle technique par rapport au plasma sont :
- Système de projection plus simple de mise en oeuvre (pas de circuit d’eau de refroidissement, un seul circuit de gaz),
Système moins cher d’investissement, - Système plus simple d’utilisation avec moins de paramètres à régler et optimiser,
Système plus robuste nécessitant moins d’intervention (changement fréquent des électrodes de la torche plasma surtout en cas de mauvais réglage) et plus adapté à des cadences industrielles avec une très bonne reproductibilité, - Moindre surchauffe du substrat (température maximum de l’ordre de 4 000 °C au niveau de l’arc électrique) très localisée à la jonction des deux fils,
- Grande variété de matériaux projetables avec en particulier l’arrivée sur le marché des fils fourrés constitués d’une âme métallique remplie de poudres,
- Bonne adhérence, en principe supérieure à celle des revêtements réalisés par plasma,
- Rendement de projection en principe supérieur au plasma (70%) et débit pondéral projeté bien supérieur (jusqu’à 40 kg/h pour certains matériaux),
- Le matériaux à projeter est stocké sous forme de fil et est donc plus facilement manipulable,
- Pas besoin de stockage de gaz (argon, hydrogène) pouvant être dangereux (le gaz utilisé est de l’air comprimé ou de l’azote qui peuvent être fabriqués sur site).
CANON À DÉTONATION
Le principe de la projection par canon à détonation consiste à utiliser la détonation ou les ondes de choc résultant de l’explosion contrôlée d’un mélange oxygène / carburant pour fondre et projeter la poudre du matériaux sélectionné sur la pièce à revêtir.
Le système est complexe. En opération un mélange de la poudre à projeter, d’acétylène et d’oxygène est injecté dans la chambre de détonation qui débouche sur une tuyère d’un mètre de long et 2,5 cm de diamètre comme illustré sur le diagramme suivant. Les gaz de combustion peuvent être neutre, oxydants ou réducteurs, leur température peut être contrôlée soit par ajout de gaz neutre pour les refroidir ou soit par ajout d’hydrogène pour les réchauffer. Un mélange poudre / gaz mesuré et contrôlé automatiquement est injecté dans la chambre d’explosion avec un système de soupapes et allumé avec une bougie. L’onde de choc résultante accélère les particules de poudre jusqu’à environ 750 m/s et produit des températures pouvant atteindre 4 000°C. La pression générée par la détonation ferme les soupapes de contrôle jusqu’à ce que la pression dans la chambre soit uniforme. A la suite le cycle est répété entre 4 et 8 fois par seconde. Entre chaque cycle la chambre est purgée à l’azote ou à l’air comprimé. Chaque détonation dépose un couche très dense et très adhérente de plusieurs microns d’épaisseur et d’environ 2,5 cm de diamètre. La répétition des cycles conduit à des revêtements épais. Un tel équipement génère beaucoup de bruit, environ 150 dBA, et doit être utilisé dans une cabine insonorisée.
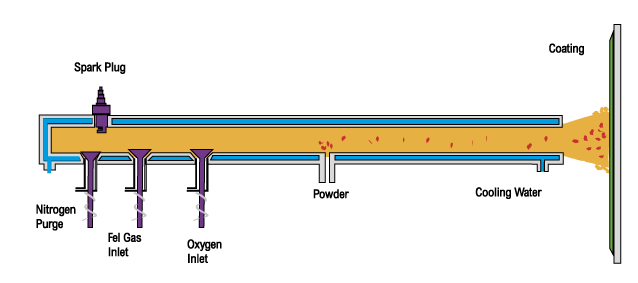
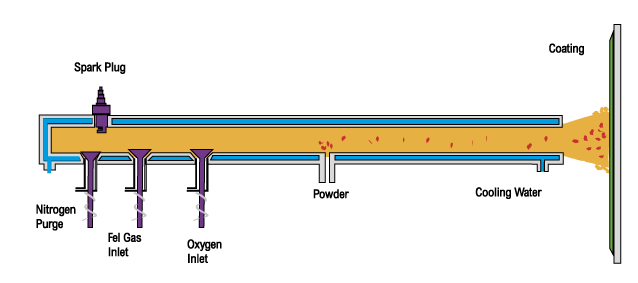
LA PRÉPARATION DU SUBSTRAT AVANT REVÊTEMENT
S’il y a une étape que l’on peut qualifier de très importante dans le processus de projection thermique, c’est bien la préparation du substrat. Tout comme tous les autres procédés de déposition ou de revêtements de surface comme le soudage, l’électro-plating, l’émaillage ou la peinture, une préparation non satisfaisante peut être pénalisante pour l’adhésion du revêtement sur son substrat. A titre d’exemple dans le cas d’un substrat en aluminium ou l’un de ses alliages qui ont la particularité d’être recouverts d’une couche infime d’oxyde (Al203) très stable, cette dernière doit être détruite pour favoriser un bon accrochage du revêtement sur son substrat. Deux voies sont possibles, un traitement mécanique (sablage par exemple) ou un traitement physico-chimique, le revêtement devant être réalisé dans la continuité.
De nombreux travaux ont été réalisés pour trouver la meilleure préparation relative au meilleure accrochage des revêtements sur leur substrat. Les trois méthodes suivantes donnent les meilleures résultats :
- Le nettoyage et décapage chimique,
- Le sablage avec un abrasif (corindon par exemple), (voir figure suivante),
- La préparation par usinage : elle consiste à réaliser une forme de filetages (voir 2ème figure suivante) sur la surface à traiter. Ce type de préparation correctement menée donne une très bonne adhérence et a l’avantage d’être réalisée directement dans la continuité de l’opération d’usinage de la pièce.
- La préparation avec une sous-couche d’accrochage. Dans la plupart des cas l’adhésion est mécanique (voir figure). Cependant avec certains matériaux comme le Nickel-Aluminium Ni5Al, l’Aluminium-bronze, l’accrochage avec la plupart des métaux est métallurgique, il est normalement supérieur à la cohésion du dépôt lui même (des tests de traction conduisent à la dé-cohésion dans le revêtement et non à l’interface dépôt-substrat). De part ces propriétés exceptionnelles, ces matériaux peuvent servir d’accrochage entre le revêtement final et le substrat. Diverses méthodes peuvent être retenues pour la préparation de la surface avant projection de la sous-couche. Elles sont :
- l’attaque chimique,
- le sablage (cette méthode a l’avantage de réduire les contraintes de fatigue), le procédé donne une surface propre et satisfaisante,
- l’usinage même s’il est très grossier,
- le meulage grossier avec une meule à gros grains conduit à un bon état de surface pour la projection de sous-couches d’accrochage comme le Ni5Al.
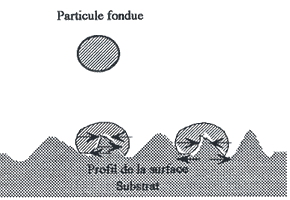
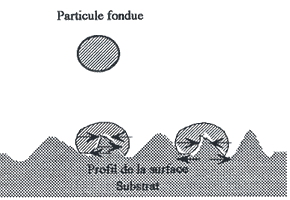
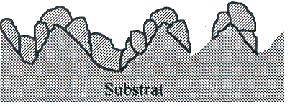
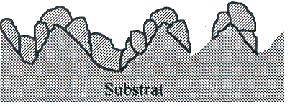
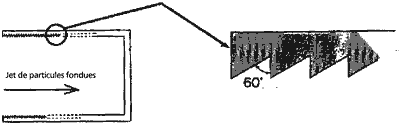
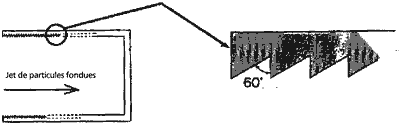
MÉTHODOLOGIE DE RÉALISATION D'UN REVÊTEMENT
Réaliser un revêtement suivant l’état de l’art nécessite toute une démarche qui peut être illustrée par le diagramme suivant et par le recensement des différentes phases successives :
- Analyse du problème de surface à résoudre : elle doit aboutir à la définition du cahier des charges du revêtement à mettre en œuvre,
- Le choix du matériaux du revêtement : Il est sélectionné en fonction des contraintes du problème,
- Le choix de la technique de projection : elle est sélectionnée en fonction du matériau sélectionné et des caractéristiques du revêtement recherché,
- Le choix de la technique de préparation de surface : elle doit être compatible avec le substrat traité,
- La définition de l’épaisseur optimale du revêtement : elle est définie par le composant et ses sollicitations de fonctionnement. Dans le cas d’une surface qui subit de l’usure, l’épaisseur minimale est déterminée par le maximum d’usure autorisé et une épaisseur minimale de dépôt uniforme, et aussi essentiellement par le coût. Le surplus d’épaisseur nécessaire à l’usinage final ou à la rectification ou rodage doit être correctement estimée ; il est important d’apprécier que si à la suite de l’usinage final la côte n’est plus bonne pour l’utilisation de la pièce traitée, toute l’opération de traitement de surface est à refaire, il faut donc prévoir une marge de sécurité. La rugosité du revêtement est alors un paramètre à prendre en compte pour la mesure des épaisseurs déposées. Typiquement des épaisseurs de 150 microns à plus d’un millimètre (voir plusieurs millimètres dans le cas de certains matériaux et certaines techniques de projection),
- La nécessité du masquage : il est nécessaire pour empêcher le métal projeté d’adhérer sur les parties de la pièces qui ne doivent pas être traitées. Il est généralement appliqué après l’opération d’usinage avant le sablage ou la projection de la sous-couche. Il peut être sous forme de rubans adhésifs, de produits appliqués au pinceau ou par spray ou alors particulièrement dans le cas de production sous forme de parties métalliques pouvant être clipsées,
- La réalisation du revêtement,
- L’éventuel « re-traitement » du revêtement (recuit, application d’un polymère agent de colmatage de porosités, usinage, rodage, mise à la côte, affinage de la rugosité…),
- La caractérisation du revêtement : elle est réalisée sur une éprouvette témoin ; le revêtement peut être caractérisé d’un point de vue laboratoire en terme de morphologie-microstructure, porosité (taille des pores et distribution), micro-dureté, adhérence, structure cristalline, … ou d’autres tests spécifiques comme les évaluations des caractéristiques thermiques (diffusivité et conductivité thermiques, dilatation), des caractéristiques thermiques (résistivité électrique, tension de claquage), des tenues à l’usure (abrasion sèche ou humide, érosion, cavitation, …), de résistance à la corrosion (tests de brouillard salin), aux acides…Notons néanmoins que même si ces caractérisations permettent d’avoir une bonne idée du comportement du revêtement, elles ne remplacent pas son évaluation en conditions réelles de fonctionnement. Elles permettent aussi un suivi qualité.
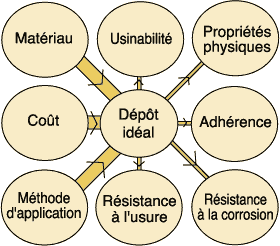
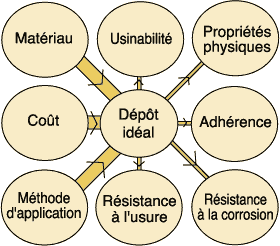